New Tobacco Products – Nicotine Pouches Production Process
Nicotine Pouch NEWS
New Tobacco Products – Nicotine Pouches Production Process
As a prominent category within smokeless tobacco products, nicotine pouches significantly reduce harmful substances generated from tobacco combustion and pyrolysis. These pouches can be used in smoke-free environments such as indoors and on airplanes, meeting consumers’ physiological need for nicotine intake. Currently, nicotine pouches are particularly popular in Northern European countries like Sweden, Norway, and Denmark, as well as in markets like Russia and the United States.
According to a recent report by the market research and consulting firm Maximize Market Research Pvt Ltd, the global market size for oral tobacco products is expected to reach nearly $23.6 billion by 2030, with an astonishing compound annual growth rate (CAGR) of 35.8% between 2024 and 2030. This indicates a promising market outlook.
Common nicotine pouches are typically made by mixing granules or powders. Depending on moisture content, they can be classified into three types: dry, semi-dry, and wet products. Based on humidity levels:
• Low-humidity products: Moisture content below 8%.
• Medium-humidity products: Moisture content between 8%-25%.
• High-humidity products: Moisture content above 25%. In Europe, high-humidity products account for more than 80% of the market due to their quick onset and strong throat hit.
However, high-humidity products often face challenges during production due to poor flowability from excess moisture, leading to uneven pouch content, clogging of packaging machinery, and reduced production efficiency.
Leading Product Types:
• Dry Process: Represented by ZYN, with a moisture content of less than 3%.
• Semi-Dry Process: Represented by FEATX, with a moisture content between 3-8%.
• Wet Process: Represented by VELO, further subdivided into:
• Low-humidity products: Moisture content 8%-10%.
• Medium-humidity products: Moisture content 8%-20%.
• High-humidity products: Moisture content above 20%.
Nicotine Pouch Production Process
Process Flow:
Granulation → Automatic Tray Sorting → Pouching → Counting & Filling → Tray Placement → Lid Sealing → Labeling → Heat Shrink Packaging → Collection

1.Weighing:
Based on specific requirements (e.g., flavor, cooling effect, sweetness), the ingredients are weighed accordingly. The nicotine composition typically includes nicotine, sugar alcohols, pH adjusters, fillers, purified water, binders, humectants, flavorings, and dispersants

2.Granulation:
Powders, flavorings, nicotine liquids, and aqueous solutions are mixed with binders and subjected to radial, axial, and tangential movement in a modified blender for thorough mixing. The mixture is then granulated into uniform, dense spherical particles (visible granules in the pouches) using a granulating cutter.Granulation Methods:
Granulation Methods:
- Wet Granulation
- Dry Granulation
- One-Step Granulation
- Spray Granulation
Among these, wet granulation is the most widely used.

3.Pouching:
The granules from the previous step are fed into a hopper above the packaging machine. The feed rate is controlled by a photoelectric positioning device. Non-woven fabric rolls are guided through rollers into a forming collar, folded, and longitudinally sealed into flat shapes. The material is automatically metered and filled into the formed pouches.
The horizontal sealer performs heat sealing or ultrasonic cutting while intermittently pulling the pouch cylinder downward, forming three-sided sealed flat pouches. A PLC system ensures precise control of metering, filling, and sealing.
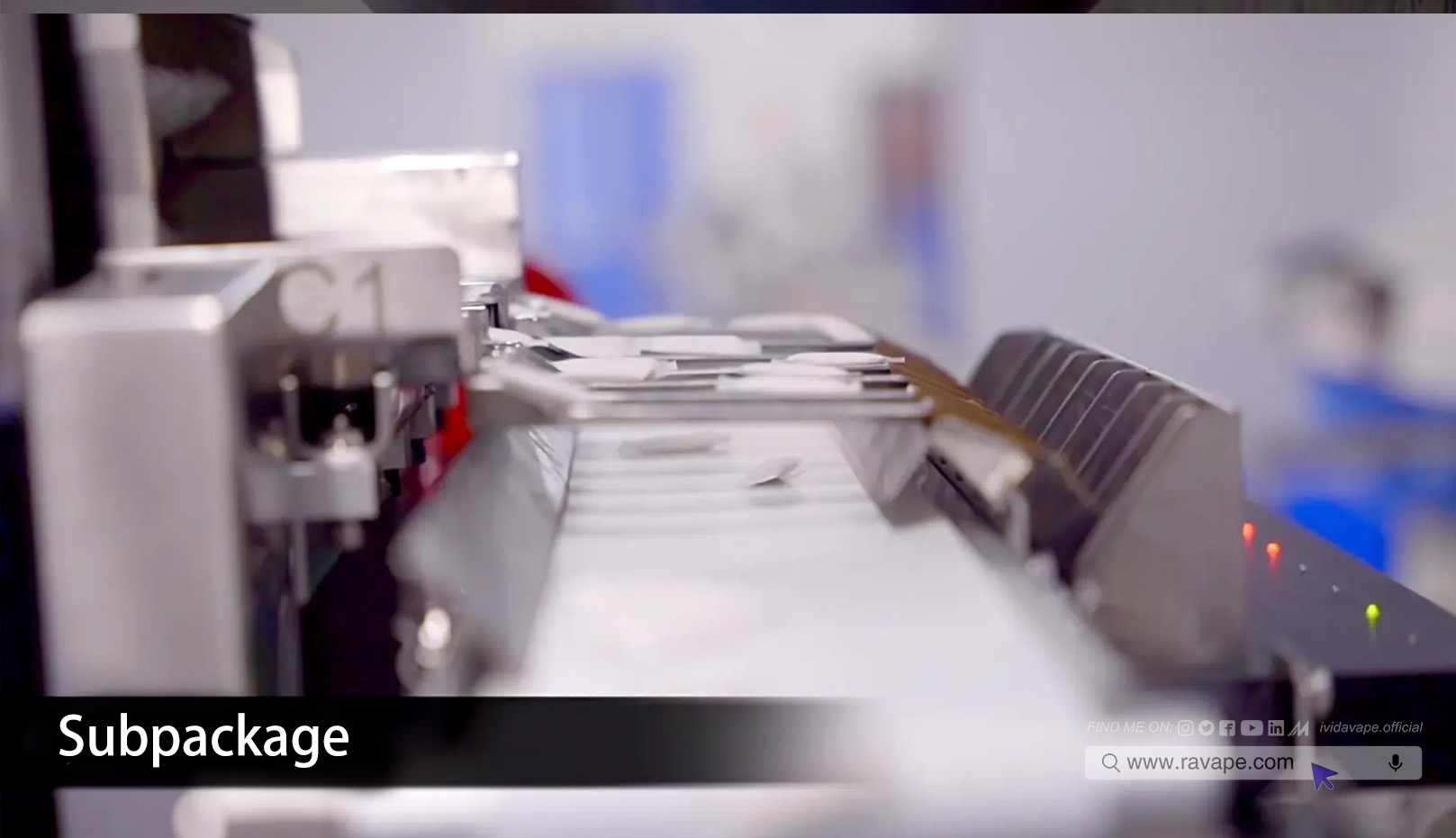
4.Filling:
The pouches are packed into cans based on requirements. Common cans are typically 7cm in diameter and hold 15, 16, 18, or 20 pouches per can. Additionally, boxes may be either white or black. For the IVIDA brand, 20 pouches per can is standard.
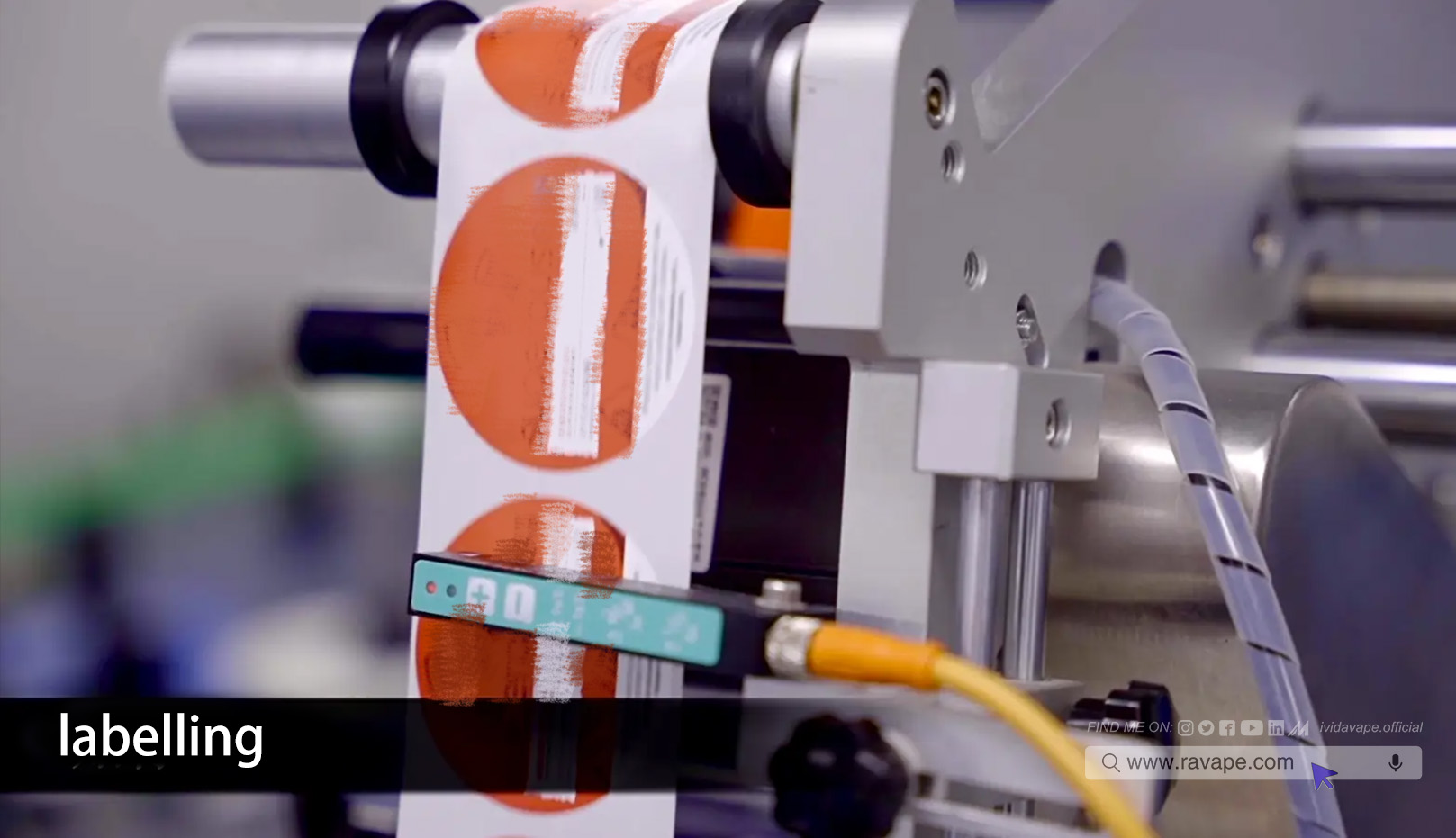
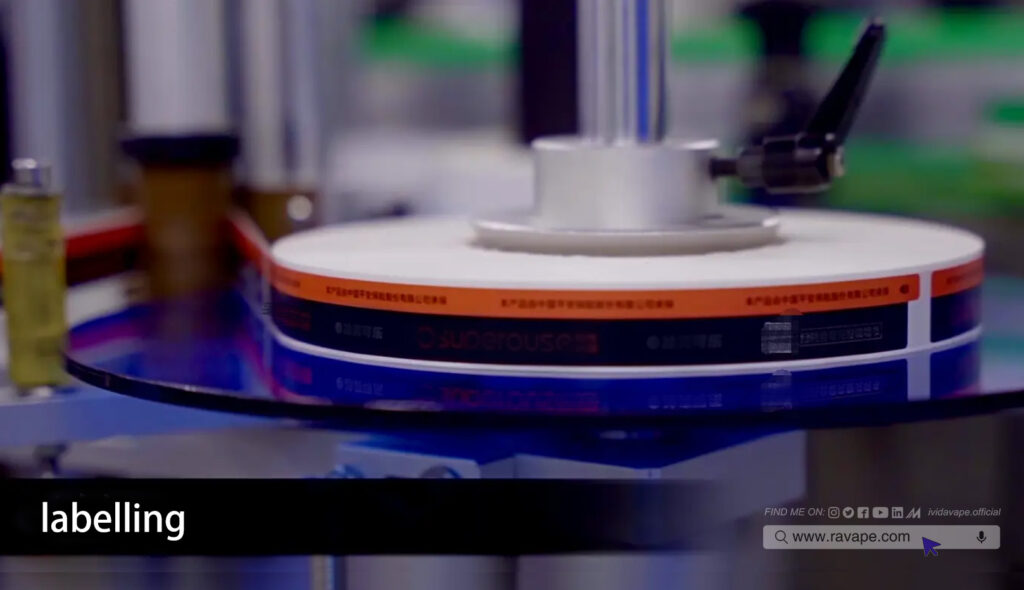
5.labeling:
Different brands require different labels. Round cans typically have labels on the front, back, and sides.
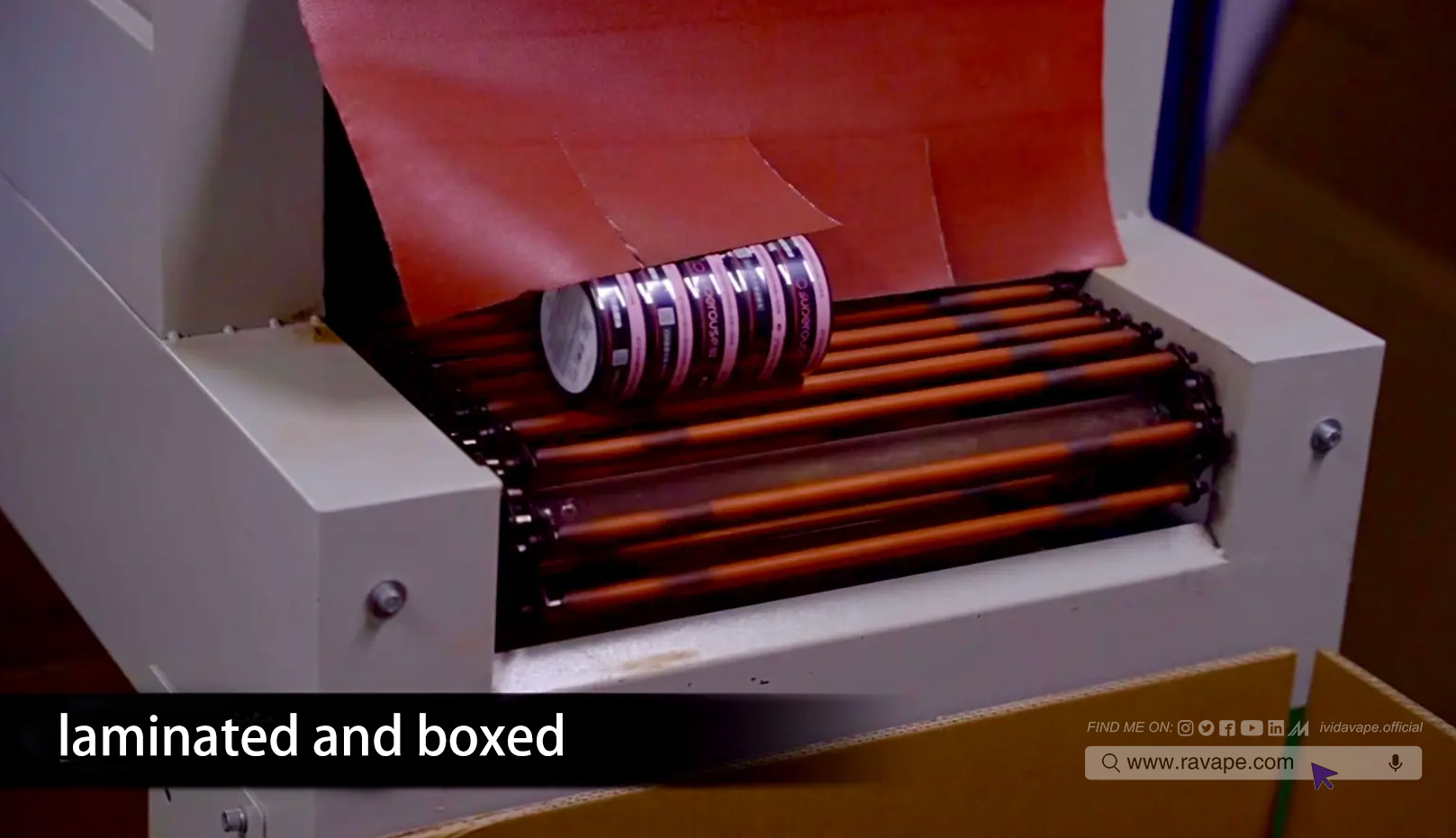
6.Shrink Wrapping:
Packaging varies by brand, with common configurations being 5 cans per pack or 10 cans per pack.
Key Components in Nicotine Pouch Manufacturing
The nicotine pouch industry is attracting increasing attention due to its immense growth potential. However, industry experts reveal that only a few companies produce high-quality products. Essential factors include production equipment, packaging materials, and key components like non-woven fabric, cans, labels, and raw materials. 1. Production & Packaging Equipment: The structure of nicotine pouches is relatively simple, consisting primarily of nicotine, flavorings, stabilizers, and fillers packed into non-woven fabric pouches sealed with heat or ultrasonic technology. 2. Non-Woven Fabric: The fabric must meet medical-grade standards, with appropriate density to prevent leakage while ensuring good permeability. By emphasizing high-quality materials and advanced production techniques, companies can achieve consistent product quality and optimize production efficiency.


3条评论
已关闭评论。